In suitable applications, hot dip galvanizing provides ideal corrosion protection for steel – no other coating matches galvanizing’s unique combination of low initial cost, ease of inspection for coating quality, durability, predictable performance, low maintenance and resistance to abrasion and mechanical damage.
Hot dip galvanizing is often perceived to be more expensive than it is. There are two reasons for this: Firstly, that such a high performance coating is automatically assumed to be expensive. Secondly, the initial cost of galvanizing relative to paint has changed significantly over recent years. Painting costs have steadily increased whilst galvanizing costs have remained stable.
Parts of virtually any size and shape can be galvanized depending on the handling facilities available at the galvanizing plant. Most items to be hot dip galvanized will be suspended from a jig and/or overhead crane using wires, chains, brackets or hooks while being processed.
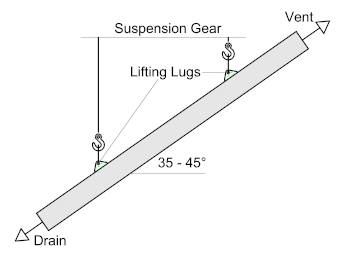
The maximum size and weight that a particular galvanizer can process should always be checked at the design stage.
For long items, adequate hanging points should be provided, e.g., suspension holes or lugs, taking into consideration article size and the lifting capacity of equipment.
For long, straight sections, 2 lifting lugs are preferred to avoid wire or chain marks. Where possible, articles are suspended at an angle of between 35° and 45° to ensure efficient drainage of pre-treatment solutions and molten zinc.
Small items such as fasteners, nuts and brackets may be placed into baskets rather than hung. Items longer or deeper than the bath size may be galvanized by using a double-dipping method. See ‘Double dipping process’ for more information. In these cases, material handling considerations will impact on cost. A better method may be to use bolted connections or modules for assembling post galvanizing.
How it Works
The reaction of the molten zinc during the hot dip galvanizing process provides a coating that is metallurgically bonded to the steel. The result is not a simple coating, but rather a series of hard iron/zinc alloys which become more zinc rich towards the outer surface of the coating. These alloys provide an adherent coating that is harder than the underlying steel providing good resistance against mechanical damage. Also, the coating tends to thicken around corners that tend to be thinly coated using other corrosion protection compounds.
Should an exposed area of steel be evident, the zinc surface will preferentially corrode at a slow rate protecting the steel – this is known as Cathodic Protection and where the damage is small, the protective corrosion products of the zinc will fill the exposed area arresting attack.
Should the mechanical damage be severe exposing the steel beneath, the surrounding zinc will protect against Corrosion Creep (attack under the coating) which is common with other coatings where the rust spreads from any damaged area.
The Galvanizing Process
There are a number of steps in the galvanizing process which include:
- The cleaning cycle – decreasing and chemical clean
- Fluxing – helps to wet the surface of the steel
- Galvanizing – immersion of steel into bath of molten zinc
- Post treatment (optional)

The Cleaning Cycle
Degreasing
Organic surface contaminants, such as oils and some paint, are carefully removed from the steel by suitable preliminary treatment, usually via a caustic solution. Some paints, lacquers and oils may need to be removed prior to the arriving at the galvanizing plant.
Pickling
After degreasing, the steel undergoes pickling or acid cleaning to remove rust and any mill scale. Hydrochloric acid is most commonly used for this purpose, although sulphuric acid is also used.
Fluxing
The acid-cleaned steel article is then immersed in a flux solution, containing zinc ammonium chloride, and usually operating at 50-70°C. The flux solution removes any oxide film which forms on the steel surface after acid cleaning, preventing further oxidation before galvanizing and activating the surface. The work is then dried ready for galvanizing.
Galvanizing
Prepared items are galvanized by immersion in molten zinc. On immersion in the galvanizing bath the steel surface is completely covered by the molten zinc, which reacts with the steel to form a series of zinc-iron alloy layers. The thickness of these layers is determined principally by the mass of the steel being galvanized. This is an important advantage of the galvanizing process – a standard minimum coating thickness is applied automatically regardless of the operator.
To allow formation of the coating the work remains in the bath until its temperature reaches that of the molten zinc, in the range of 445°C to 465°C. The work is then withdrawn at a controlled rate and carries with it an outer layer of molten zinc which solidifies to form the relatively pure outer zinc coating.
With proper venting and draining design, the molten zinc covers corners and welds, seals edges, and penetrates recesses to give complete protection to areas which are potential corrosion spots with other coating systems. The galvanized coating is usually slightly thicker at corners and narrow edges, giving greatly increased protection compared to organic coatings which thin out in these critical areas. Complex shapes and open vessels may be galvanized inside and out in one operation.
The period of immersion in the galvanizing bath varies from a few minutes for relatively light articles, or longer for very heavy structural members.
Post Treatment
Upon extraction from the galvanizing bath the article is normally cooled via a quench solution, which usually contains an inhibitor to provide passivation of the zinc surface to prevent early oxidation.
For reasons of aesthetics or environments which are particularly corrosive, the items may be either painted or powder coated, in which case further surface preparation may be required. Before any surface preparation takes place, the galvanizer should be notified the steel will be painted. With this understanding, the galvanizer will forego any post-treatments that could affect paint adhesion and take special care in delivering a surface suitable for painting or powder coating.
Further information on the required surface preparation can be found in ASTM D6386 Standard Practice for Preparation of Zinc (Hot-Dip Galvanized) Coated Iron and Steel Product and Hardware Surfaces for Painting and ASTM D7803 Standard Practice for Preparation of Zinc (Hot-Dip Galvanized) Coated Iron and Steel Product and Hardware Surface for Powder Coating.
Double Dipping Process
Double dipping is a term used to describe the process of galvanizing an item which is longer, wider or deeper than the relevant available bath dimensions. In this procedure, the item is lowered into the bath so that half or more of its ‘over dimension’ is immersed in the molten zinc.
When the galvanized coating has been achieved on the immersed section, the item is withdrawn from the bath and adjusted in handling so that the ungalvanized portion can be immersed in the molten zinc.
The coating thickness is the same as the normal galvanizing process – it is not ‘double’.
Galvanizing Smaller Items
Fasteners and small components are loaded into perforated cylindrical steel baskets. After acid pickling and fluxing, baskets are lowered into the galvanizing bath. On withdrawal from the molten zinc, baskets are raised without delay into a centrifuge or ‘spinner’ and rotated at high speeds for 15 to 20 seconds. Excess zinc is thrown off, providing a smooth, uniform coating and maintaining the integrity of threaded items.
The coating thickness and mass requirements differ from other batch galvanized pieces due to the spinning process removing excess zinc.
The size of baskets, centrifuges and other equipment will vary, just like general galvanizing baths.
Note: Not all galvanizers have centrifuge facilities and not all small items will be galvanized via the centrifuge process.